Check out these automotive interior mold manufacturing images:
Manufacturing
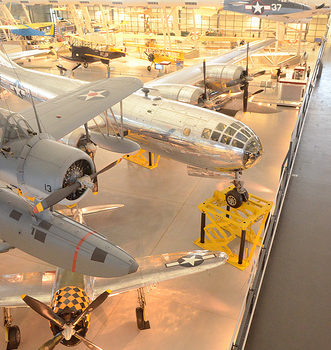
Cool Auto Mould Manufacturing images
Some cool auto mould manufacturing images:
Steven F. Udvar-Hazy Center: South hangar panorama, including Vought OS2U-3 Kingfisher seaplane, B-29 Enola Gay
Image by Chris Devers
Quoting Smithsonian National Air and Space Museum | Vought OS2U-3 Kingfisher:
The Kingfisher was the U.S. Navy’s primary ship-based, scout and observation aircraft during World War II. Revolutionary spot welding techniques gave it a smooth, non-buckling fuselage structure. Deflector plate flaps that hung from the wing’s trailing edge and spoiler-augmented ailerons functioned like extra flaps to allow slower landing speeds. Most OS2Us operated in the Pacific, where they rescued many downed airmen, including World War I ace Eddie Rickenbacker and the crew of his B-17 Flying Fortress.
In March 1942, this airplane was assigned to the battleship USS Indiana. It later underwent a six-month overhaul in California, returned to Pearl Harbor, and rejoined the Indiana in March 1944. Lt. j.g. Rollin M. Batten Jr. was awarded the Navy Cross for making a daring rescue in this airplane under heavy enemy fire on July 4, 1944.
Transferred from the United States Navy.
Manufacturer:
Vought-Sikorsky Aircraft Division
Date:
1937
Country of Origin:
United States of America
Dimensions:
Overall: 15ft 1 1/8in. x 33ft 9 1/2in., 4122.6lb., 36ft 1 1/16in. (460 x 1030cm, 1870kg, 1100cm)
Materials:
Wings covered with fabric aft of the main spar
Physical Description:
Two-seat monoplane, deflector plate flaps hung from the trailing edge of the wing, ailerons drooped at low airspeeds to function like extra flaps, spoilers.
• • • • •
Quoting Smithsonian National Air and Space Museum | Boeing B-29 Superfortress "Enola Gay":
Boeing’s B-29 Superfortress was the most sophisticated propeller-driven bomber of World War II and the first bomber to house its crew in pressurized compartments. Although designed to fight in the European theater, the B-29 found its niche on the other side of the globe. In the Pacific, B-29s delivered a variety of aerial weapons: conventional bombs, incendiary bombs, mines, and two nuclear weapons.
On August 6, 1945, this Martin-built B-29-45-MO dropped the first atomic weapon used in combat on Hiroshima, Japan. Three days later, Bockscar (on display at the U.S. Air Force Museum near Dayton, Ohio) dropped a second atomic bomb on Nagasaki, Japan. Enola Gay flew as the advance weather reconnaissance aircraft that day. A third B-29, The Great Artiste, flew as an observation aircraft on both missions.
Transferred from the United States Air Force.
Manufacturer:
Boeing Aircraft Co.
Martin Co., Omaha, Nebr.
Date:
1945
Country of Origin:
United States of America
Dimensions:
Overall: 900 x 3020cm, 32580kg, 4300cm (29ft 6 5/16in. x 99ft 1in., 71825.9lb., 141ft 15/16in.)
Materials:
Polished overall aluminum finish
Physical Description:
Four-engine heavy bomber with semi-monoqoque fuselage and high-aspect ratio wings. Polished aluminum finish overall, standard late-World War II Army Air Forces insignia on wings and aft fuselage and serial number on vertical fin; 509th Composite Group markings painted in black; "Enola Gay" in black, block letters on lower left nose.
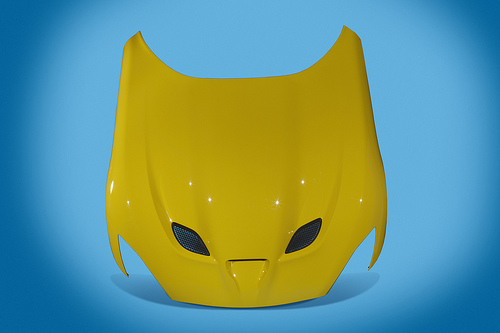
Nice Automotive Mould Manufacturing photos
Check out these automotive mould manufacturing images:
Nomination 42 – Body Exterior – View A – Carbon Composite Hood Assembly
Image by spe.automotive
CARBON COMPOSITE HOOD ASSEMBLY
•OEM Make & Model: Chrysler Group LLC 2013 model year (MY) SRT Viper® supercar
•Tier Supplier/Processor: Plasan Carbon Composites
•Material Supplier / Toolmaker: Umeco plc/Cytec Industries (carbon fiber weave prepreg); Toray Carbon Fibers Americas, Inc. (unidirectional carbon fiber prepreg); Ashland, Inc. (structural polyurethane adhesive) / Weber Manufacturing Technologies Inc.
•Material / Process: G83C T700S-24K carbon composite / Vacuum bag, autoclave cure
•Description: This hood assembly is a Class A CFRP part with a very large complex clamshell geometry. The painted Class A outer panel is complemented by an exposed weave inner panel. The part represents the largest Class A carbon fiber composite part provided to a mainstream OEM at volumes up to 3,000 vehicle sets/year. Design, tooling, and fabrication technologies from both marine and aerospace were employed for the first time in automotive to facilitate layup of the complex geometry with severe undercuts. Integrated mounting points using riv-nuts and studs are molded into the inner hood panel. Local section thickness was varied to meet structural requirements. The final part, incorporating fenders as well as hood is 44% lighter than the previous hood-only assembly in SMC, helping improve weight distribution and lower the vehicle’s center of gravity, for better vehicle dynamics and power-to-weight ratio.
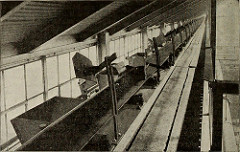
Professional Plastic Pvc Molding Technology Is the New Manufacturing Benchmark
The plastic pipes are most demanding and most required necessity of our daily life. These PVC pipes are made by highly professional technicians that needs perfect design and raw material that can guarantee best quality and longevity of these products. These are made through optimal heat treatment technology that provides desired quality control. These are made under the supervision of engineers in a plastic factory under the proper guidelines designed by the industry experts and experienced professionals.
The engineering staff of the mould manufacturing constantly reviews and analyzes the complete manufacturing process as every aspect of the process is significant in achieving the desired results such as plastic pipe moulds. Do products like plastic pipe fitting mould require such an attention? Considering the sensitivity and their finer applications, it is recommended to have close monitoring of their manufacturing. They are generally designed by experienced mould designers and technicians those who put in their efforts in core processes such as the hot- runner and the cold- runner mould mechanisms, also by applying software applications like auto CAD, UG, PRO/E, solid works free that are known for their advantage in mould manufacturing.
What else happens in a plastic mould factory? In a factory these moulds are further made by quite high quality and advanced equipments that are used for the measuring, digital control cutting machines, electric spark and precise tools that are quite efficient to work for the preparation of these moulds. These efforts are made to ensure the calibration levels are precisely achieved.
Products that are manufactured as the pipes and their fittings:-
What are mainly manufactured plastic pipe fitting mould products? The manufactured products are like that of the plastic fitting moulds that are like the PVC pipe fitting moulds, PPR pipe fitting mould, PE pipe fitting mould, ABS pipe fitting moulds, PPSU pipe fitting moulds and there are even many other kinds of fitting moulds that are yet to develop.
Evaluating the durability standards of plastic pipes
The durability of these pipes and fittings depends completely on their manufacturing process where they are under strict surveillance by the manufacturing unit. Do we have any surveillance guidelines for a plastic mould factory? There are guidelines and recommendations by the international manufacturing councils that are applicable for molding factories too. Accordingly, these manufacturers handle these processes with collapsible core demolding system that consists of the core and the cavity that are the main parts of the mould structure. And they consist of fixed bars in the main core which is provided with a sliding rail outside and there is an active cavity for the installation of the stiffening ribs next to the fixed bar.
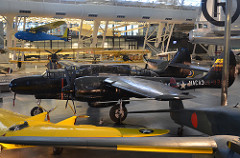
Mould Manufacturing in China Is All about Perfection
These Plastic moulds are the frames that are used to make the medical instruments and other instruments related with their building in the plastic business like that of the syringes. These are quite the professional plastic mould makers who are associated with the designing as well as building of these plastic moulds. These moulds are made with utter guidance and perfection as they are required to present the perfect measurement of the syringes and other types of plastic moulds that will hold the medicine into it.
How distinguished a China mould manufacturer is? These mould generating businesses are been famously know for incorporating the suggestions of clients who are have numerous priorities of making sure the launch of higher top quality items and grow to be normal to develop worth for their respective organizations. They might be either little scale or even massive scale manufacturing organization in the China offer exceptional manufacturing solutions in the arena of molding. What relevance does a plastic mould maker China has? These plastic based mould producers are the organizations that are quite much on demand in the present trade driven market. Their mission is to be the greatest mould makers and to assist their clients to bring their item to market faster and overcome the competition in the most price effective manner.
They perform for a number of kinds of solution development or plastic merchandise design and manufacturing. These companies specialize in the manufacturing of precision production moulds, custom molded plastics and the integrated options. Most of these companies are related with the services that are efficiently known as injection molding solutions.
It needs a complete professional method
To prepare these plastic moulds these expert teams function with specialized engineering departments where they apply latest 3D strong modeling CAD program technology that is utilised to develop a conceptual design and style for generating the prototype samples that are additional necessary for the manufacturing of the plastic moulds. Does a plastic mould maker China need to have a temperature controlled atmosphere? Yes, molding techniques are all about thermodynamics and sufficient temperature upkeep is the important to any greatest outcome. This process of mould producing involve machinery like that of micrometer, digital calipers, project machine, CMM, wire cut, EDM machine, high speed CNC and a secured workshop where these moulds are to be created.
Best utility and applications of molding technologies
How the knowledge of a China mould manufacturer is place to ideal use? Molding processes are applied in several purposes like that of medical appliances and apparatus producing, medicine bottles, syringes and numerous a lot more these are even utilised into the generating of thermoforming molds, die castings, aluminum molds and the prototype moulds.
Discover A lot more China Mould Make Solutions Producers Articles
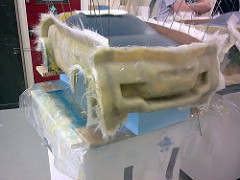
Intricacies of Processing and Manufacturing of the Automobile Plastic Components
The automobile parts and the injection moldings are the demanding merchandise of the plastic business exactly where there is standard workout of these two simple merchandise. The injection moulding is the 1 that are utilised to make the thermoplastic and the thermosetting polymers. And the automotive components are plastic parts that are utilised for the building of the automotives like that of the car assembly components, body for the door lock latches, door and damper ,vehicle door handles, and numerous far more plastic molded components.
How injection mouldng producers produce distinctive items? These are made by melting the plastic and then remolding them into the desired frame under a stress that topic it to reframe. These merchandise are the outstanding architects of the plastic injection producers who style the moldings to facilitate the moulding process. These products are made by an industrial designer or any plastic engineer who are the tool makers of these moulds from the metals that are either the steel or aluminum and these are precision – machined to from the characteristics of the preferred element.
What significance do automotive components moulding have? They are created with the 3D printing of the injection moulds by the use of photopolymer plastics that do not melt during the injection process. These have a variant use in the construction of the automotive parts moldings.
What are these utilised for?
Exactly where plastic injection moulding makers are utilized? These moldings are utilised to create many things like that of the wire spools, packaging, bottle caps, automotive dashboards, pocket combs and even utilised to make specific components of the musical instruments. It’s now very the frequent a single that is used for the manufacturing of the products associated to the automotives.
How are these moulds developed?
What are the simple components of automotive components moulding? These moulds are designed with the two simple elements that are required for the automotive moulding which are that of the injection mold and the ejector mold. These two are made to operate combined as the plastic resin is made to enter the mold through a gate in the injection mold and is busing is to seal tightly against the nozzle of the injection barrel of the machine to permit the flow of the molten plastic in to the mold from the barrel and then the gate bushing directs the molten plastic to the cavity images through channels that are machined into the faces of the A and B plates.
And following that these channels allow the plastic to run along them and the molten plastic flows by way of the runner and enters a single or more specialized gates and into the cavity. This type of mechanical perform is even guided by the authorities who perform to analyze the qualitative survey of these moldings.